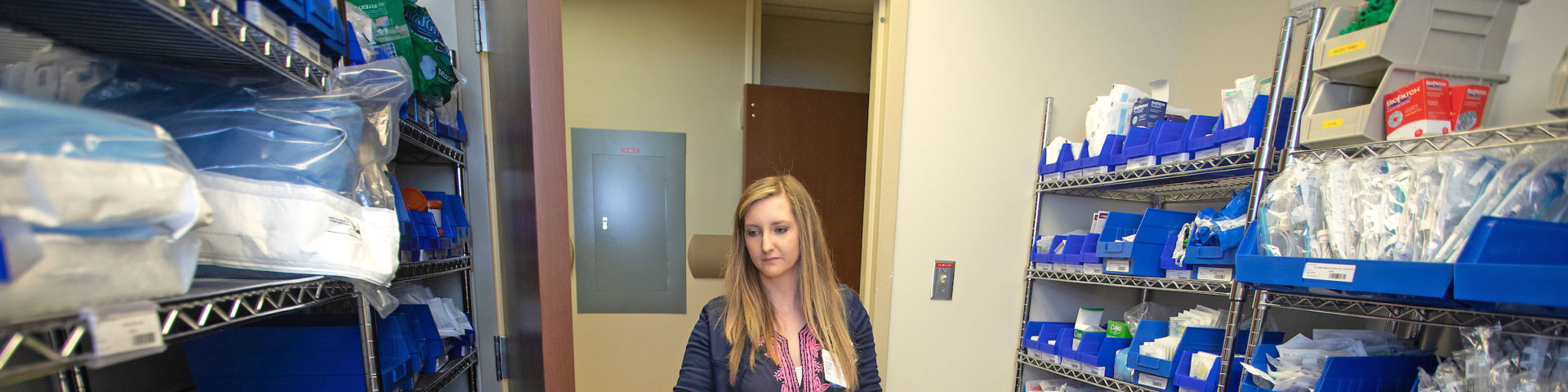
Unified materials management helps USA Health respond to COVID-19
A new centralized approach to materials management ensured that the hospitals and clinics used the same types of supplies, from wound dressings to ports and tubing.
When USA Health launched an effort to standardize purchasing, supply processing and distribution across the health system in 2016, the intent was to improve continuity of care. A new centralized approach to materials management ensured that the hospitals and clinics used the same types of supplies, from wound dressings to ports and tubing.
No one knew it , but the move four years ago would prepare USA Health to respond better to the current COVID-19 pandemic.
“Having a centralized system allows us to move inventory around to where it is needed the most,” said Chase Labrato, director of materials management for USA Health. “For instance, we are able to divert masks and gowns from idle operating rooms to other places to protect patients and employees,” he said.
Still, with healthcare systems worldwide buying unprecedented amounts of personal protective equipment, the usual amount might not even be available. In February, USA Health was notified that it should expect back orders on PPE from Hubei province, the home of Wuhan and the first cases of the novel coronavirus.
It was time to get creative. “We are working with nontraditional vendors,” Labrato said. “We’ve had to think outside the box.”
When Mobile- based Calagaz Printing retooled its shop to create clear face shields for healthcare workers, USA Health was in on the decision-making. “They brought in a design, and we said, ‘Yes, this looks good,’” Labrato said.
University Hospital and Children’s & Women’s Hospital each received 2,500 of the Calagaz face shields.
USA Health also connected with a California company in the fashion industry that had been vetted by the Association for Healthcare Resources & Materials Management. The company helped to facilitate orders for protective isolation masks from a manufacturer in Asia.
In the meantime, USA Health’s implementation of a two-bin inventory system at University Hospital has helped manage inventory. For each supply, departments are allotted two bins – each with a four-day supply level. As the first bin is emptied, it is placed on a top shelf, where it is noted by a storekeeper who makes rounds, scans codes for needed items and places orders to restock. The efficient process has saved both time and money, he said.
Labrato said that lessons learned during the COVID-19 crisis will help inform decisions to come. “In the future, I think you’ll see more supplier risk assessments being done for commodity-type items such as masks and gloves,” he said. “For now, we’re not out of the woods yet, but employees conserving PPE continues to help us stretch our supplies.”